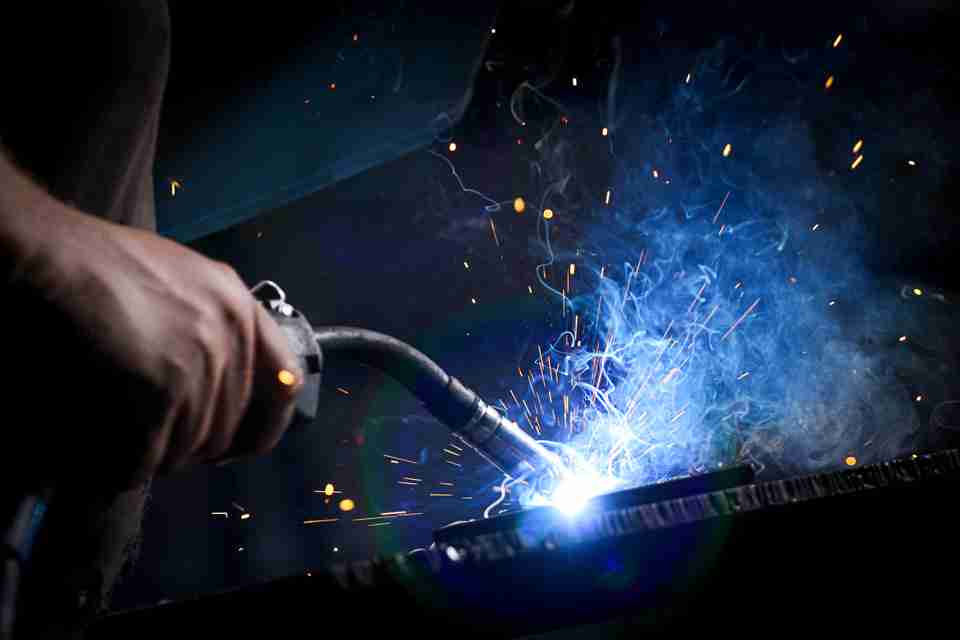
Recent reports about faulty welds impacting U.S. naval infrastructure performance highlight the increasingly important value of welding quality. This imperative extends across all industries, serving as a stark reminder to prioritize quality control measures and regulatory compliance.
Welding Gaffes Threatening Maritime Operations
In September 2024, shipwright company Newport News Shipbuilding informed the Department of Justice of violating proper welding procedures on in-service submarines and aircraft carriers. Despite the defects primarily affecting noncritical components, the issue has warranted a congressional review and a wider investigation into quality assurance protocols.
Alarmingly, this is not the first instance of defective weld issues in the Navy. In 2019, officials discovered inferior welding on missile tubes in hunter-killer subs. Aside from the obvious safety issues and increased risk to onboard personnel, the scandal of such occurrences in the military proves the pervasiveness of flawed welds.
Welding Defects in Other Sectors
These problems may even be more pronounced in other industries. In the automotive space, BMW North America recently recalled several vehicles manufactured between 2023 and 2025 due to welding defects compromising braking systems.
In a related development, Amazon issued a return request for school classroom stack chairs, citing weld failures in the frame, which pose a fall hazard.
The direct cost of these recalls can easily run into millions, sometimes billions of dollars, depending on the scale and impact of the defect. There are also legal fees and compensations to consider. Beyond the immediate financial implications, recalls can erode consumer trust, leading to long-term consequences for the company’s market position and bottom line.
How Welding Quality Impacts Product Durability
The influence of welding quality on a product’s sturdiness and reliability is profound, impacting critical areas over time.
Structural Integrity and Fatigue Resistance
Defects directly impact the structural integrity of joints and related components due to the inherent loss of fatigue strength in the welding process.
According to a study on medium-carbon steel welding, fatigue resistance can drop by 40%-60%, significantly increasing the likelihood of premature failures in critical applications. For instance, inadequate weld quality leads to cracks forming at stress points, ultimately compromising the structure’s load-bearing capacity.
Corrosion Susceptibility
Poor welding practices can render welded structures more susceptible to corrosion. An analysis of a pipeline failure attributed to improper welding procedures revealed that the lack of fusion in weld joints allowed corrosive agents to penetrate the metal. These effects can be devastating, especially if multiple leaks appear simultaneously at different locations along the pipeline walls.
Loss of Tensile and Impact Strength
Burn-through defects in welding applications have significant implications for the mechanical integrity and performance of welded components. The resulting tensile strength reduction presents substantial safety concerns, primarily when implemented in everyday projects like transportation and construction.
Research shows porosity and incomplete fusion from flawed welded joints reduce tensile capacity by 2.7% compared to defect-free operations. These issues also decrease impact strength resistance, rendering the connected areas more susceptible to mechanical failures under load and increasing the risk of sudden fractures.
Long-Term Implications on Life Span
Subpar welding quality extends beyond immediate structural concerns to impact the overall service life of machinery and equipment. It’s one of the primary reasons quality assurance in industrial settings involves ensuring welded seams meet the requirements for safe, long-term operations.
Best Practices for Ensuring Higher Weld Quality
Achieving and maintaining the highest weld quality standards demands a comprehensive approach encompassing meticulous practices and innovative technologies. The following strategies present a viable foundation for implementing scalable defect-prevention initiatives across diverse industries.
1. Robust Training and Certification
Continuous hands-on learning is an essential first step in cultivating a skilled weld workforce. The American Welding Society (AWS) offers comprehensive training and certification programs for welders to enhance their skills and knowledge.
These sessions also instill several performance attributes, including accountability, workmanship and professionalism, which often differentiate between quality and shoddy job output.
2. Enhanced Quality Control and Inspections
Imperfections like cracks, porosity and incomplete penetration that could compromise weld integrity are often difficult to identify. Implementing regular nondestructive testing procedures, such as ultrasonic testing and radiography, can detect welding defects early in the fabrication process.
This proactive approach ensures the quality of welds, minimizing the risk of costly rework and potential failures in service.
3. Advanced Welding Methods
Embracing advanced welding methods is a pivotal best practice for enhancing weld quality, especially where conventional techniques might not be as effective. For example, high-frequency welding generates heat from within the material itself, producing welds that match or even exceed the strength of the surrounding materials.
This method is particularly advantageous in plastics and PVC manufacturing, where precise and consistent welds are paramount for structural integrity and performance.
4. Pre-Weld Preparation and Material Selection
Thoroughly cleaning base materials removes contaminants that can lead to defects like porosity and lack of fusion. Additionally, selecting materials with compatible compositions and mechanical properties reduces the likelihood of cracking and enhances the overall weld quality.
Employers must require welders to pay meticulous attention to these preparatory steps, setting the stage for durable and reliable welds that meet the highest quality standards.
5. Outsource to Robots
Adopting collaborative robots, or cobots, represents a cutting-edge best practice for enhancing weld quality. Cobots excel in precision welding tasks, offering consistent performance and eliminating human errors.
This ability has been shown to enhance production output by up to 300% while reducing employee fatigue, leading to better workplace safety.
What’s Next for the Global Welding Market?
The welding market is poised for a 4.5% CAGR between 2024 and 2030. The key drivers include the growing demand for welded products, design flexibility and ease of modification.
At the same time, challenges such as skilled labor shortages, fluctuating raw material costs and increasing environmental regulations pose hurdles to market growth.
Embracing digitalization, upskilling the workforce and leveraging innovative welding technologies present avenues for stakeholders to navigate these issues and capitalize on emerging opportunities.
Higher Welding Quality Is Nonnegotiable
The persistence of weld defects in just about every industry represents an urgent call to action for leaders to prioritize quality assurance and safety measures. Having explored the repercussions of subpar welding practices, emphasizing the importance of adhering to stringent standards has never been more paramount.
Emily Newton is the Editor-in-Chief of Revolutionized Magazine, an online publication that explores innovations in science and technology.